K-factor
Overview
When a metal sheet is bent with a press brake, its material is deformed, which is the reason for the difference in overall length of a sheet in folded and unfolded states. BricsCAD automatically considers this deformation when you unfold a sheet metal part. Two approaches are used to compute it: a simplified one (K-factor) and a more advanced one.
The material deformation properties for bending is based on the assumption that there is internal surface for the sheet metal part which is not deformed when the sheet is bent. From the variety of internal surfaces, one surface is selected which is equidistant from one side of the bend. The surface is local for each bend, and for simple cases it can be propagated on entire part, like the one in the picture. We assume that this surface is not stretched during bending.
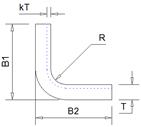
T: thickness of the sheet metal part
R: internal radius of the bend
The K-factor (k) is the ratio of the location of the neutral surface to the material thickness. As a result, the neutral surface lies at a distance kT from the internal surface of the bend. The bend radius of the neutral surface equals R + kT. The K-Factor is a simple geometric calculation of the location of the neutral surface. Forming stresses and other unknown (error) factors are not considered. The K-Factor depends on many factors, such as the kind of material, bending type and tools. The K-Factor typically lies between 0.3 and 0.5. The default K-Factor for a bend radius equal to the material thickness (T) is 0.27324.
In the unfolded state of a sheet metal part, the flanges (L1 and L2) are not stretched. The bend part is indicated as BA: Bend Allowance. The BA equals the length of the unfolded neutral surface:
Bend Allowance: BA = BendAngle * (R + kT)
In fact, it is hard to measure the K-factor or the bend allowance. The following formula allows to calculate the tangential Bend Deduction (BD):
Bend Deduction: BD = B1 + B2 - Unfolded Length = B1 + B2 - (L1 + L2 + BA)
For simple cases, the K-Factor value can be overridden in the Mechanical browser. For maximal precision a bend table containing tangential bend deductions has to be provided. For each sheet metal part, you can either specify a K-factor or use the default one.
Changing the K-factor for a Sheet Metal Part
To change the K-Factor for a sheet metal part, select the root node in the Mechanical Browser and type a value in the K-Factor field. The value must lie in the range [0, 1], since the neutral surface is located inside the sheet metal part. In BricsCAD the K-Factor is defined for bend radius equal to the material thickness (R/T = 1). To compute the value of K-Factor for an arbitrary bend radius, BricsCAD uses a special interpolation technique which is proved to be valid for industrial sheet metal applications. The image below shows the interpolation strategy: for R/T < 1 the linear interpolation is done between 0 and 0.27324, for 1 < R/T < 4 the K-Factor is linearly interpolated between 0.27324 and 0.5 and if R/T is greater than 4, the K-Factor is constant and equals 0.5. Physically it means that if the bend radius is much larger than the thickness (at least 4 times), the material stretch is neglected.
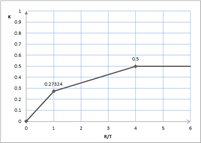
The only K-factor parameter you can control in the Mechanical browser is for R/T=1. That means if you set the value to 0.6, the interpolation law leads to the following result:
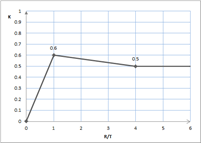
Pic: the varying K-factor in the browser leads to the following effective curve.
The distinguishing feature of the curve is that varying R in range of (0, T], L1 + L2 + BA gives the same value. This reflects the fact that for radii less than the thickness they relate to are for design convenience rather than for some physical process modeling, since during bending tool radius is usually greater or equal to thickness.
Let us review the example with varying K-factor by control curve setting (the bend radius is kept constant).
T = 2, R = 2, B1 = 100, B2 = 100
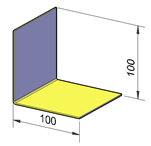
Setting K=0 gives L1=L2=96, Unfolded Length = 195.14, thus BA is 3.14.
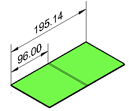
This value fits the formula exactly: a straight angle in radians roughly equals 1.57 (PI/2). The default K-factor 0.27324 gives an Unfolded Length = 196.
Or: L1=L2=96 (flanges are not deformed), the BA = 4 as we can compute from the dimensions (196 - 2*96) or from the Bend Allowance formula:
BA = BendAngle * (R + kT) = 1.57 * (2 + 2*0.27324) = 4
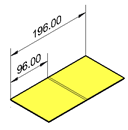
Finally, maximizing K-factor results in an Unfolded Length = 198.28. This is the maximal value one can achieve in this example since the neutral surface is taken from the external side of the bend.
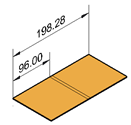
The Bend Deduction (BD) for k = 0.27324:
BD = B1 + B2 - Unfolded Length = 100 + 100 - 196 = 4