Piping in Assembly Design
Overview
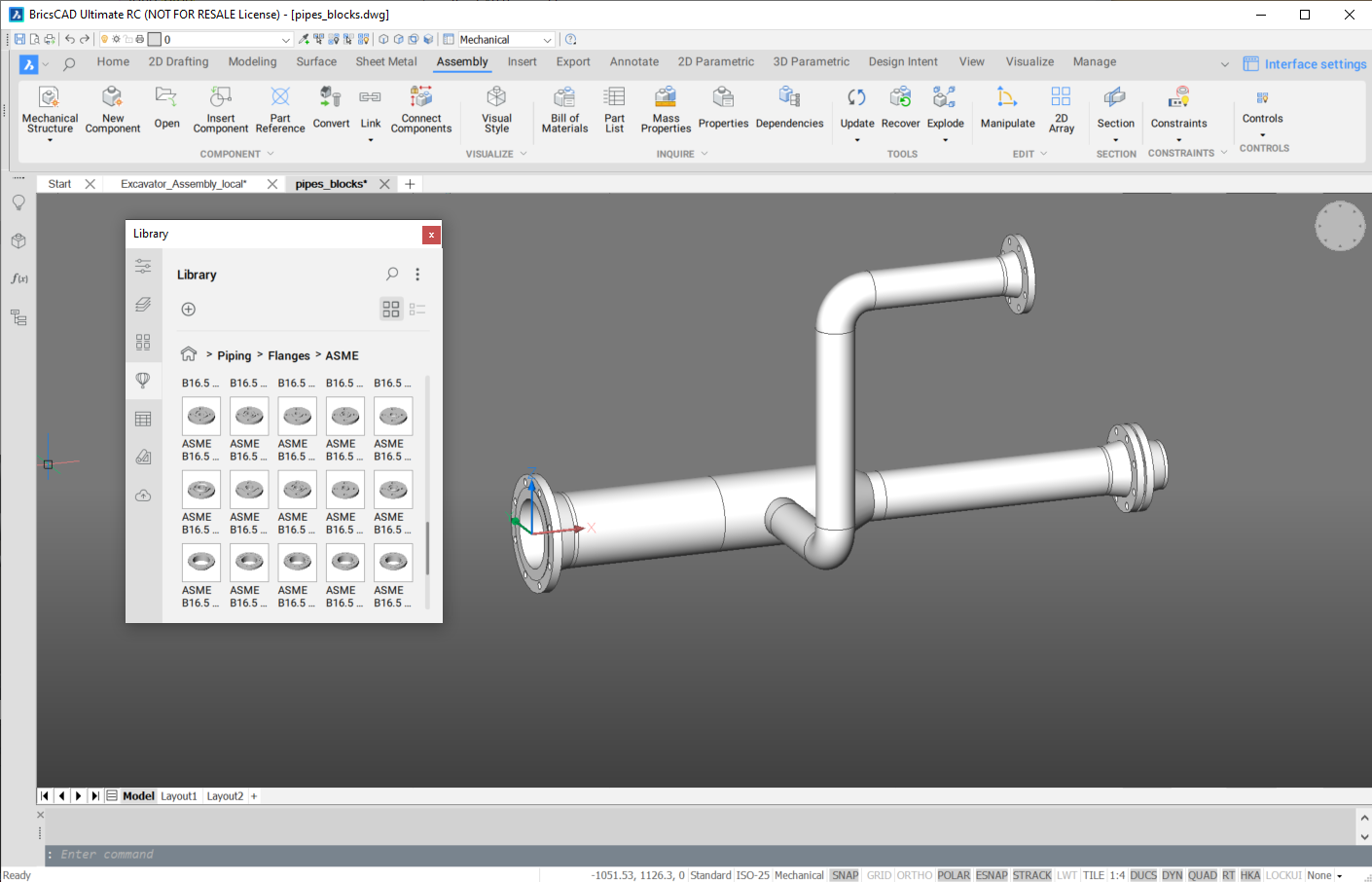
Seamless and welded pipes, elbows, tees, crosses, reducers and flanges are widely used in machinery, automotive, and aviation industries. They are also found in oil-and-gas, chemical industry, and water supply. BricsCAD® has a library of parametric piping parts of different standards, such as ASME, DIN, and ISO. These standard parts are parametric. You can easily adjust their parameters, link them to different global parameters, and use 3D constraints to properly connect the parts. BricsCAD® allows you to streamline these routine operations using the Smart mode of the BMINSERT command and a dedicated BMCONNECT command.
Insert piping parts in your assembly
Drag and drop any piping standard part from the Library panel into your assembly.
- Copies parameter expressions of that part to the corresponding parameters of the part being inserted.
- Adds a set of 3D constraints to connect the parts.
Create 3D constraints between piping standard parts manually
Piping standard parts have a set of wireframe entities (points and lines) on the STD_PARTS_PIPING_CONNECTION layer, which is switched off by default.
Constraining a fitting
- 2 points of the fittings, which should coincide
- 2 lines of the fittings, which should be collinear.
Constraining a pipe
Constraining pipes is more complex because a pipe can have any length. If a pipe is already constrained with a fitting at one side using 2 Coincident 3D constraints, then constraining it from the other side must be different.
- A Coincident 3D constraint between the line, which represents the axis of the pipe, and the corresponding line of the other fitting
- A geometry-driven Distance 3D constraint between the planar face of the pipe on the opposite (already constrained) side and the corresponding point of the fitting, which is being connected.
You must then type the name of the distance constraint in the expression field for the Length parameter of the pipe. Because geometry-driven constraints allow controlling of a particular dimension, the pipe will always have the correct length, and such a parametrization will not limit any further editing of your assembly using direct manipulation of additional non-geometry-driven dimensional constraints.
Automatically connect piping parts
The set of constraints is created automatically using the Smart mode of BMINSERT command or the dedicated BMCONNECT command to connect 2 standard parts.
Create a Bill of Materials for a piping assembly
In a BOM you may want all pipes of the same type and size (PartNumber), but with different lengths, listed as the same part
Use the Aggregate function of the BOM Manager to combine all such parts in a single row with their total length.